Why Digital Fabric Printing is the Future of Textile Design
- Soundarya
- Feb 22
- 4 min read
Updated: Feb 25
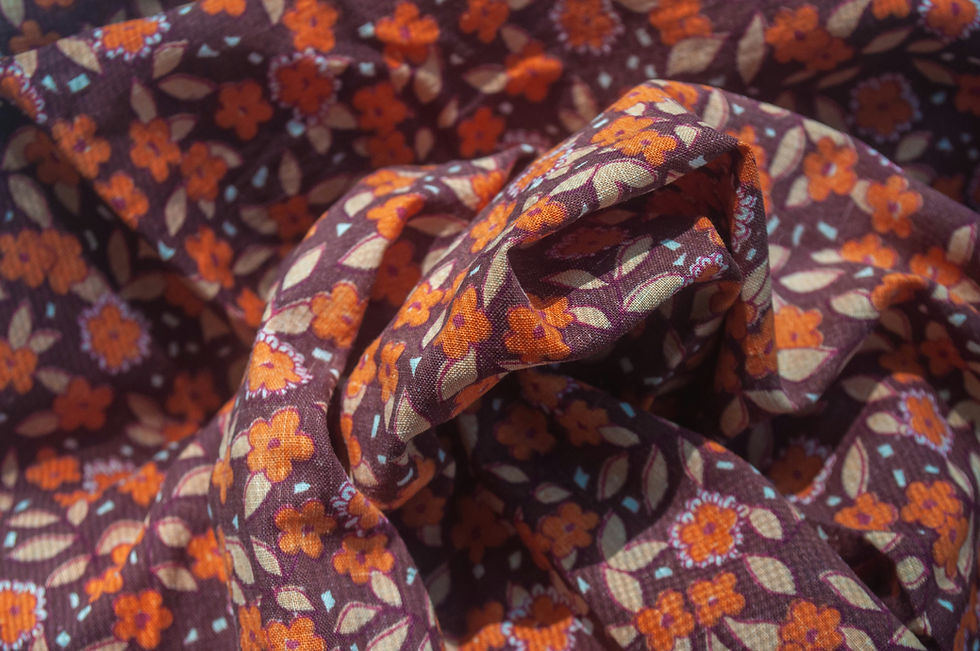
Digital fabric printing is a cutting-edge textile printing method that uses inkjet technology to apply designs directly onto fabric. Unlike traditional methods that rely on screen printing and dye sublimation, digital printing allows for intricate, high-resolution designs with minimal setup time.
Fabric printing has evolved significantly over the centuries. From block printing in ancient times to rotary screen printing in the 20th century, the industry has continuously adapted to technological advancements. Digital printing emerged in the late 20th century and has rapidly gained traction due to its efficiency and creative possibilities.
Importance in the Textile Industry
Digital fabric printing has revolutionized textile manufacturing by offering flexibility, efficiency, and sustainability. Compared to traditional methods, which require extensive setup and large-scale production, digital printing allows for small batch production and customization, catering to modern consumer demands.
Industry trends indicate a growing preference for personalized fashion, sustainable practices, and automation, all of which align with digital fabric printing’s capabilities. Brands are increasingly adopting this technology to meet fast-changing consumer expectations.
Scope of the Article
This article explores the advantages, technological innovations, real-world applications, and future potential of digital fabric printing. Readers will gain insights into how this technology is shaping the textile industry, from designers and manufacturers to consumers seeking unique, sustainable, and high-quality fabrics.
Advantages of Digital Fabric Printing
Design Flexibility
One of the primary benefits of digital fabric printing is its design versatility. Designers can create intricate patterns and gradients that are difficult or impossible to achieve with traditional printing techniques.
Furthermore, digital printing enables rapid prototyping, allowing designers to test and iterate designs quickly without significant material waste or high costs.
Sustainability Considerations
Sustainability is a crucial factor in modern textile production. Digital fabric printing significantly reduces waste since it does not require screens, plates, or excess dye. Additionally, many digital printers use water-based, eco-friendly inks that minimize environmental impact.
The shift toward sustainable fashion and textiles has driven increased adoption of digital printing methods. By reducing resource consumption and enabling on-demand production, digital printing supports ethical and sustainable manufacturing practices.
Cost-Effectiveness
Traditional fabric printing methods involve high setup costs, making them economically unfeasible for small production runs. Digital printing eliminates these barriers by allowing for on-demand production, reducing inventory costs, and enabling small businesses to compete with larger manufacturers.
For businesses, digital printing translates to reduced waste, lower production costs, and the ability to offer customized products without excessive investment.
Technological Innovations in Digital Fabric Printing
Advancements in Printing Technology
Modern digital fabric printers feature advanced capabilities such as multi-color printing, high-speed production, and enhanced precision. Software improvements have also played a crucial role, enabling designers to create and manipulate complex designs with ease.
Emerging technologies, such as 3D printing combined with textiles, are opening new possibilities in fabric design, enhancing the aesthetic and functional aspects of printed textiles.
Material Innovations
A wide range of fabrics can now be digitally printed, including cotton, silk, polyester, and blends. Innovations in ink formulations, such as reactive and pigment inks, have expanded the range of compatible textiles, enhancing durability and color vibrancy.
Additionally, smart textiles—fabrics embedded with technology—are being explored in conjunction with digital printing to create interactive and functional clothing.
Real-World Applications of Digital Fabric Printing
Fashion Industry
Digital fabric printing has become a staple in the fashion industry, with brands using it to create unique designs and limited-edition collections. Major fashion houses and independent designers alike have embraced the technology for its speed and precision.
Runway shows increasingly feature digitally printed fabrics, showcasing the limitless creative possibilities of this technology.
Home Decor and Interior Design
Beyond fashion, digital fabric printing is transforming home decor. Upholstery, curtains, bed linens, and wall coverings can now be customized with intricate patterns and vibrant colors.
Interior designers benefit from this flexibility, offering clients personalized decor solutions that were previously difficult to achieve with traditional fabric printing methods.
Specialty Markets and Custom Products
Digital fabric printing is also making waves in niche markets such as sportswear, promotional merchandise, and custom apparel. Small businesses can produce unique, high-quality printed textiles without the financial burden of bulk production.
The rise of direct-to-consumer business models has further fueled demand for digitally printed custom products, allowing brands to cater to individual customer preferences.
Future Outlook for Digital Fabric Printing
Market Growth Projections
The digital fabric printing market is experiencing rapid growth, driven by technological advancements and changing consumer behaviors. Analysts predict continued expansion, with increasing adoption across fashion, home textiles, and industrial applications.
Challenges such as ink costs and fabric compatibility remain, but ongoing innovations are addressing these barriers.
Evolving Consumer Preferences
Personalization is a key driver of digital printing's growth. Consumers are increasingly seeking unique, custom-made products, a trend fueled by social media and e-commerce platforms.
Sustainability concerns are also shaping consumer choices, making eco-friendly printing methods more appealing to both brands and buyers.
The Role of Collaboration
Collaboration between designers, manufacturers, and technology companies is essential for driving innovation in digital fabric printing. Partnerships with educational institutions can further train the next generation of textile designers, ensuring continued advancements in the field.
By fostering a community of creative and technological synergy, the textile industry can maximize the potential of digital printing for future generations.
Conclusion
Digital fabric printing is revolutionizing the textile industry with its design flexibility, sustainability benefits, and cost-effectiveness. As technological innovations continue to enhance the process, its applications across fashion, home decor, and specialty markets will only expand.
Manufacturers, designers, and businesses that embrace this shift will position themselves at the forefront of a more sustainable, efficient, and creatively limitless future.
Frequently Asked Questions (FAQs)
Q: What are the main differences between digital and traditional fabric printing? A: Digital printing offers greater design flexibility, lower setup costs, and reduced waste compared to traditional methods.
Q: How does digital fabric printing contribute to sustainability? A: It minimizes water and ink waste, supports on-demand production, and uses eco-friendly inks.
Q: Can digital fabric printing be used for large production runs? A: While traditionally suited for small batches, advancements are making it viable for large-scale production.
Q: What types of materials can be printed digitally? A: A wide range, including cotton, silk, polyester, and specialty blends.
Comments